Electric Motors and Industrial Efficiency: Innovation is Key for EVs
Electric motors can be found in everything from cars to toothbrushes. Electric motors-and the systems they use- account for more than 40% of global electricity consumption, according to the International Energy Agency. However, their design and technology have remained largely unchanged for decades. Today, that is changing. Various drivers are spurring innovation in electric motors, including:
- Projected growth of electric vehicles
- Energy efficiency standards in HVAC systems
- Rising demand for efficient energy use from conventional sources -such as coal and natural gas- and industrial electricity production.
In 2011, the IEA estimated that 25% of electric motor-driven system (EMDS) electricity use could be saved cost-effectively, reducing global electricity demand by 10%.
In electric vehicles, the battery is the most expensive component and limited range is a concern for many applications, such as electric buses and long-haul trucking. Although R&D efforts have mostly been focused on improving the energy density of batteries to improve range, improving efficiency of the motor itself will allow for a more efficient use of the battery as well as an extended range (and a reduction of the size) of battery required. Furthermore, efforts to make electric motors smaller and lighter will enable promising new applications such as electric planes.
In industrial and HVAC systems, compliance with Minimum Energy Performance Standards (MEPS) is driving demand for more efficient motors. Without efficiency improvements, global energy consumption from electric motors is expected to rise by 13,360 TWh annually by 2030. Some innovators claim up to 60% reduction in HVAC system energy use, which could significantly curb rising energy consumption.
Innovation is improving electric motors in five key ways:
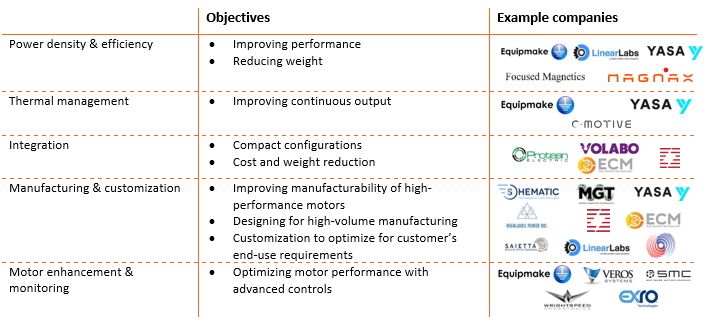
Power Density and Efficiency
In addition to torque density, power density and efficiency are key variables in improving motor performance. Improving power-to-weight ratio while maintaining high efficiency is important for endurance in electric aircraft and vehicles if they are to reduce the size of the battery needed. Power density is also key for increasing peak power, or the maximum power output (expressed as kW/kg)
Some key innovators improving power density are Linear Labs, Focused Magnetics, Magnax and YASA. The motor developed by Linear Labs does not include end windings, resulting in 30% copper savings (to reduce unproductive volume). Focused Magnetics, a company still in stealth mode, has developed an electromagnetic version of a Halbach array to focus nearly all magnetic energy towards the airgap to enhance power and efficiency and minimize losses. Magnax and YASA have both designed highly efficient and manufacturable axial flux motors, a type of motor that features high efficiency but historically has been difficult to manufacture.
Thermal Management
More electrically dominant propulsion systems lead to higher-power duty cycles for drive systems, and thermal constraints place limitations on motor performance. Innovative motor designs allow cooling systems to reach critical components, facilitating more efficient direct cooling. The designs also reduce losses and avoid the need for thermal management. Effective cooling is key to improving continuous power (sustained output) without overheating or needing to shut down.
C-Motive Technologies have designed an electrostatic motor that features near-lossless torque production and passive cooling. YASA’s controller features dielectric oil cooling for thermal management. The spoke architecture of the Equipmake APM 200 motor enables liquid cooling closer to critical components to increase continuous power.
Integration
Integrating the motor with transmission and power electronics delivers ultra-compact configurations for high power-to-weight ratios, makes cost and weight savings, and can eliminate connectors, cables and hydraulic connections. High vibration, reliability issues and the high cost of developing an entirely new axle have hindered integration efforts in the past, but the industry is still moving in this direction.
Protean Electric’s in-wheel motor features integrates power electronics and digital control that support both AI and cloud-based services and also includes an integrated friction brake. Infinitum Electric has integrated motor and control electronics and has developed a printed circuit board (PCB) stator for IoT connectivity and improved manufacturability. Volabo’s motor features integrated motor and power electronics and a virtual gearbox. E-Circuit Motors uses a cloud-based CAD/CAM platform that leverages PCB manufacturing to print stators for coreless axial flux motors.
Manufacturability and Customization
Motor customizations for low-volume manufacturing can get as close as possible to the end application to optimize design and manufacturing and deliver a higher-quality product. Meanwhile, the optimization for high-volume manufacturing involves using innovative software platforms and designs. Some key trends include: customization using advanced design platforms, designing for high-volume manufacturing and stackable, modular designs.
E-Circuit Motors offers a CAD/CAM platform that inputs discrete motor characteristics from the user and models an optimized PCB stator that is ready for mass manufacturing. Infinitum Electric uses fully automated manufacturing and a modular design to reduce cost and improve quality. Other companies, such as Linear Labs and Saietta Group, have designed motors specifically for low-cost, high-volume manufacturing. Shematic’s manufacturing process allows for the development of complete custom solutions from prototype to series. Modular and stackable motor design is another key trend, as seen in the motors developed by YASA, Highlands Power and Axiflux.
Motor Enhancement and Monitoring
We are seeing the application of AI, machine learning and big data analytics to analyze and optimize motor performance. Some key innovations are built-in sensors and connectivity for monitoring and optimization and the use of software controls.
Equipmake’s HSI 100 high-speed inverter offers high efficiency, high switching frequency and sensorless control of high-speed motors. Veros Systems apply machine learning and smart algorithms to increase uptime, improve efficiency and offer predictive maintenance. Exro Technologies’ application of artificial intelligence and big data analytics optimizes energy use in batteries, motors and generators; it also controls motor coils through individual coil switching. Wrightspeed’s four-speed, clutchless gearbox uses software controls instead of traditional transmission components. Software Motor Company have coupled a motor with computing technology, so it only uses energy when needed. The software controls offer dynamic monitoring and predictive maintenance capabilities.
Competition
Innovators often claim impressive performance metrics, but reliability and ease of assembly are sometimes compromised. The most successful companies offer high performance but also ensure integrity, durability and manufacturability of the motor. In addition, keeping costs down is critical for large scale manufacturing. The electric motor market is large, growing quickly and there is plenty of room for innovation across all segments.
Keep an eye on…
Many of the innovations and motors outlined here are still in the early stages of development and partnerships with incumbent OEMs and suppliers are key for proving out the technology. Due to furloughs and layoffs in the manufacturing sector, partnership activity has stalled through the second quarter of 2020. However, the potential of the technologies is substantial. Activity will likely accelerate as economies open back up and efforts to curb emissions across automotive and industrial sectors, such as those seen in California and Europe, will drive the commercialization of new motors and technologies.