Electric Hydrogen: A New Benchmark for Green Hydrogen Scale and Cost?
As we have noted over the past 12 months or so, maturation of end-use technology is introducing hydrogen into at-scale applications at an observable pace – from green steel production to ammonia (and ammonia-to-hydrogen for shipping), the flow of hydrogen molecules into the hardest-to-abate areas of the economy is accelerating. Underpinning any goals of industrial decarbonization, however, is the need for green hydrogen, hydrogen produced with energy from renewable sources.
For years we observed venture and growth investments evenly spread out across hydrogen production, handling, and end-use applications, but a shift has occurred and since 2021, hydrogen production technologies have dominated the venture financing landscape.
Figure 1. Venture & Growth Investments in Hydrogen Tech (2018-H1 2023)
*Excludes Outlier Deals >$350M
*Including Only Venture & Growth Investments: Seed, Series A, Series B, Growth Equity
Green hydrogen is produced through an electrolysis process – an electric current is used in an electrolyzer to split water (H2O) into its constituent elements: hydrogen (H2) and oxygen (O2). An electrolyzer consists of an anode and a cathode separated by an electrolyte – at the anode, oxygen is produced, while at the cathode, hydrogen is generated.
Figure 2. How Does an Electrolyzer Work?
Source: Greg Stewart/SLAC National Accelerator Laboratory
Cost-competitiveness of green hydrogen will be a function of renewables rollout and supply of cost-effective electrolyzers that can produce green hydrogen at cost parity with grey hydrogen (hydrogen produced from natural gas / methane) – delivered cost of grey hydrogen in the U.S. typically averages between $1 to $2 per kg. The critical barrier to economical green hydrogen production is the capital expenditure associated with electrolyzers – A 2020 IRENA report estimates a required 80% reduction in electrolyzer cost required to bring green hydrogen delivered to parity with grey hydrogen (see Figure 3 for assumptions).
Figure 3. Green Hydrogen Cost Reductions to Create Cost Parity with Grey Hydrogen
Note: ‘Today’ captures best and average conditions. ‘Average’ signifies an investment of USD 770/kilowatt (kW), efficiency of 65% (lower heating value – LHV), an electricity price of USD 53/MWh, full load hours of 3200 (onshore wind), and a weighted average cost of capital (WACC) of 10% (relatively high risk). ‘Best’ signifies investment of USD 130/kW, efficiency of 76% (LHV), electricity price of USD 20/Mwh, full load hours of 4200 (onshore wind), and a WACC of 6% (similar to renewable electricity today).
Based on IRENA analysis
Against this challenging backdrop, we have seen a series of announcements of electrolyzer gigafactories over the past year – indicating that some electrolyzer producers are gaining confidence in their ability to realize the delivery of cost-effective green hydrogen. Among these announcements was Electric Hydrogen’s May 2023 announcement that it would commence operations of a 1.2 GW/year electrolyzer factory in Devens, Massachusetts in early 2024.
I spoke with Dr. Supratim Das from Electric Hydrogen’s corporate development team, to unpack what is driving this hydrogen inflection point and understand where Electric Hydrogen fits into the picture.
Electrolyzer innovation in the past few years has ranged from granular formulation of materials for electrodes and membranes, to ready-to-use electrolyzer units, and electrolysis + hydrogen storage and distribution (e.g., refueling for vehicles) solutions. Electric Hydrogen’s differentiator is that the company builds systems which can deliver the lowest-cost green hydrogen to the hardest-to-abate sectors through large, fully modularized and integrated green hydrogen plants. Electric Hydrogen positions itself as an equipment manufacturer that delivers “bubble ready” plants to end users.
Electric Hydrogen is producing large-scale electrolyzer plants, 100 MW each, to plug into industrial scale projects. The company is taking aim squarely at industries with a need for a high volume of hydrogen use on-site, versus the smaller, more distributed applications like mobility and commercial buildings. The large-scale manufacturing at Electric Hydrogen’s gigafactory will allow the company to pass on its own economies of scale to its customers, who will be spreading the CAPEX of an Electric Hydrogen unit (>100MW) across huge volumes of hydrogen molecules. The commencement of operations at their Devens gigafactory will put Electric Hydrogen’s module scale at the “Stage 3” level of IRENA’s cost reduction milestone for electrolyzer deployment (and manufacturing scale at Stage 2).
Figure 4. IRENA Milestones for Four Cost Reduction Strategies (3 Stages of Deployment) for Electrolyzers
The U.S. Department of Energy (DOE) has set a target of $2/kg for green hydrogen by 2026. The cost profile of green hydrogen production tells a straightforward story – electrolyzer system cost (the key CAPEX) needs to drop by a factor of 3-4 to meet these targets. Variable O&M costs in green hydrogen production is mostly related to electricity cost and is not under the control of the hydrogen producer or off-taker.
Getting to competitive cost advantages that can be sustained over time, Electric Hydrogen has eschewed a silver bullet component or materials differentiation strategy and instead sought to tackle delivered cost of green hydrogen through what Das describes as a “silver buckshot”:
- Electric Hydrogen has re-designed proton-exchange membrane (PEM) electrolyzers to be manufactured with radically low critical minerals loading and record-breaking current density while using manufacturing methods that have already been proven at scale. The product is a single standardized unit complete with power electronics and balance of plant components that are co-optimized to run with the stack. This is in contrast with some other OEMs who might supply components (e.g., electrodes, membranes, or finished stacks) to be incorporated into a finished electrolyzer plant elsewhere.
- Electric Hydrogen has developed IP around stacks, power electronics and balance-of-plant (BoP) technologies to be used in electrolysis operations.
The net result is Electric Hydrogen’s electrolyzers can easily integrate into industrial off-takers’ operations.
A key accelerant toward cost parity with grey hydrogen and fossil fuels will be the tax credits enacted by the Inflation Reduction Act (IRA). Production tax credits for hydrogen production with renewables will reach as much as $3/kg for the lowest-carbon forms of hydrogen production. According to Das, before the IRA, green hydrogen was on track for cost parity with grey hydrogen in about 5 years, but with the new tax credits, green hydrogen produced with Electric Hydrogen’s systems (estimated at $3.5/kg before tax credits) can get there today.
Figure 5. With the $3/kg tax credit provisioned for green hydrogen in the Inflation Reduction Act of 2022, green hydrogen achieves cost parity with grey hydrogen
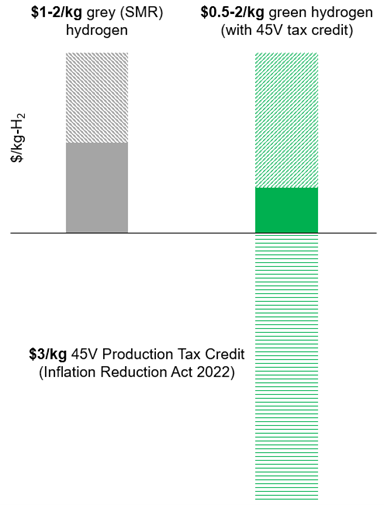
However, the grey hydrogen benchmark is just a market-clearing price at the industrial scale – long-term competitiveness will come from consistent reduction in cost through innovation and iteration. When asked about the cost competition that will almost surely arise between Electric Hydrogen and up-and-coming low-cost electrolyzer producers in China, Das shoots straight that U.S. manufacturers “absolutely will end up in a price war with China”.
Staying ahead of this challenge, Electric Hydrogen is focusing on the denominator of the $/kW equation – increasing the amount of hydrogen that can be produced by its units (i.e., higher kW), as opposed to aiming for lower-performance, cheaper materials (lower $ for the same kW). Electric Hydrogen’s goal is to keep innovating down the cost of higher-performing PEM electrolyzers to stay cheaper than incumbent alkaline electrolyzers, which use cheaper materials and are the formulation most typically produced by Chinese manufacturers.
While green hydrogen innovators have long been angling for a future market, the spate of electrolyzer gigafactory announcements over the past few months (Cummins – 500MW in Minnesota, Nel – 4GW in Michigan, Electric Hydrogen – 1.2GW in Massachusetts) means the game is on for U.S.-based producers to thread the policy needle and establish sustainable cost advantages.
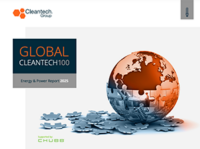